Steinhauser uses Batched as trusted system of record for data
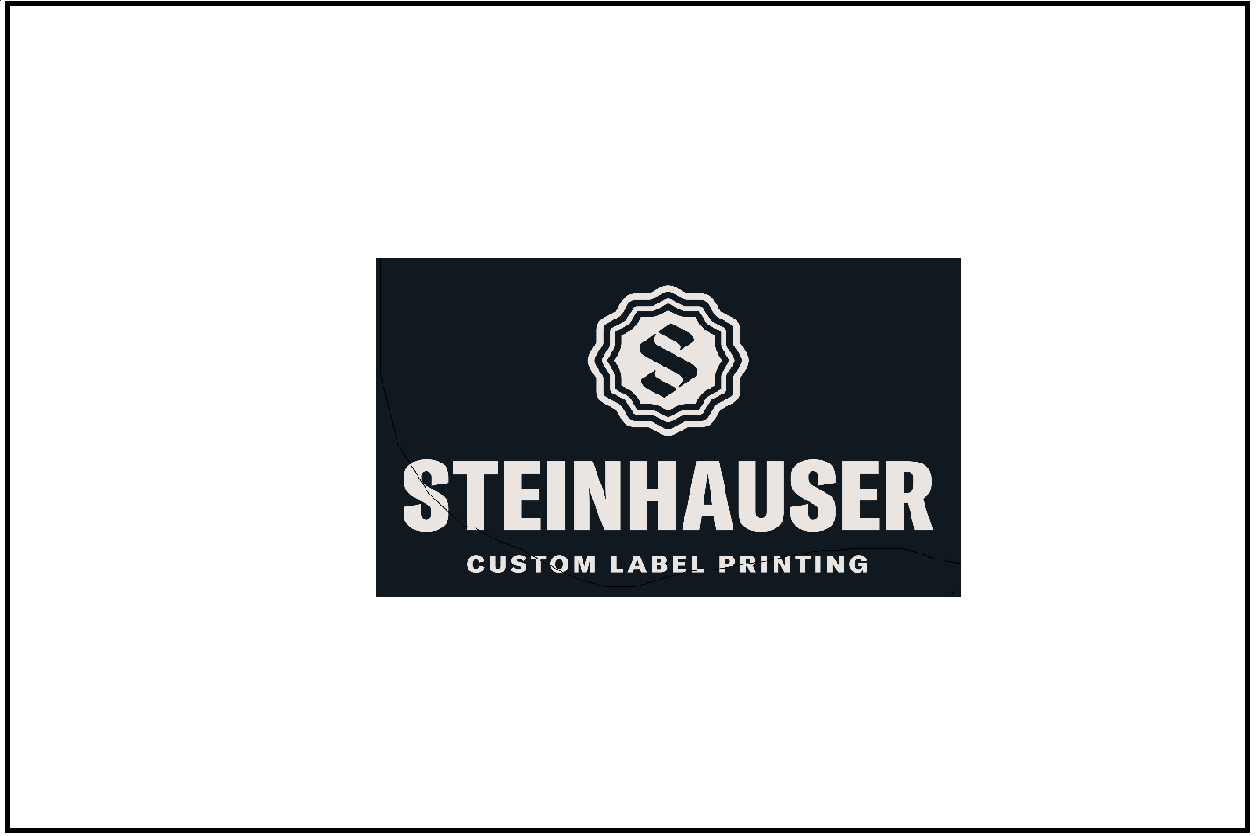
Challenges
- Increased volume, scheduling more tickets per day.
- Improved schedule management and communication with customers through reliable, precise reporting.
- Shifting from manual to automated data compilation— slower metric update frequency causing longer to shift gears when synthesizing data.
- Desire to modernize core business operations and data-driven decision making
Results
- Doubled sales
- Enhanced gross margins by ~30%
- Increase equipment utilization by more than 20%
- Maintained high on-time shipment rates despite volume growth
- Batched is now their trusted system of record for data. The primary benefit to date has been the immediate, trustworthy, actionable data.
- Operational Metrics have become predictive of financial performance
The Story
Established in 1905, Steinhauser is a fourth-generation, family-owned business. They are a regional printer based in Newport, KY, and they primarily service customers in the Midwest, South and the East Coast. Originally a commercial printer, Steinhauser pivoted to label printing in 2005. They focus on the beverage, spirits, personal care, and household markets. Under the leadership of Tara Halpin, the company has navigated various transformations, reflecting its adaptability and commitment to growth.
Their transition from commercial to label printing was a strategic move to retain a major business segment, requiring adaptation to new market demands and operational methods specific to label printing.
Operational Challenges
Steinhauser’s operational challenges during their transition to label printing included scaling up production and managing increasingly complex processes. They faced difficulties in moving from a single to a multi-shift operation, which required tighter business management and efficient coordination of resources. These challenges highlighted the need for advanced management tools to handle the growing complexity of their operations and maintain efficiency.
Implementation of Label Traxx
Steinhauser implemented Label Traxx in 2010 to address these operational challenges. Label Traxx provided them with enhanced management capabilities, allowing for more efficient scheduling, inventory control, and customer relationship management. Label Traxx’s comprehensive features helped Steinhauser streamline their operations, improve production tracking, and enabled better decision-making. This implementation of was a crucial step in modernizing their operational processes.
Adoption of Batched in 2022
In 2022, Steinhauser began using Batched for Label Traxx to further enhance their operational efficiency. Batched provided advanced data analytics and real-time monitoring capabilities, allowing Steinhauser to optimize production processes, reduce waste, and manage lead times more effectively. This technology played a pivotal role in streamlining their operations and supporting their continued growth.
“Prior to having Batched, it was a little tough to get to that without some manual tracking or a lot of data work coming out of Label Traxx,” says Rod Beahner, VP of Operations for Steinhauser. “We’ve got pretty real time data right now by equipment line that can tell us by job where we’re seeing high waste areas and allows us to react much quicker if we see a situation that is falling out of line. If we’re starting to build a trend on a particular piece of equipment or a product line, we have the ability to break it down by product, by machine, by actual material that we run. So we’ve got a much more detailed look at the operation itself to help us reduce waste.”
Impact on Operations
With their new capabilities, Steinhauser experienced more than a doubling of sales, about a 30% increase in gross margins, and over a 20% increase in equipment utilization. They also maintained high on-time shipment rates despite the increase in volume.
“We’re also very carefully monitoring our on-time delivery performance. That’s one of our key performance metrics from the service side of our business that we rely very heavily upon. That was particularly a difficult metric to get without having Batched. But again, we’ve got that real time available to us now.”
Key Metrics Used
Steinhauser utilized key metrics such as Overall Equipment Effectiveness (OEE) to gauge machine performance and downtime. This metric was crucial in understanding and optimizing their production efficiency. By focusing on these metrics, Steinhauser could more effectively manage production schedules, reduce waste, and improve lead times. This focus on data-driven decision-making was instrumental in enhancing their operational performance.
“Probably one of the most useful tools that we have that I use on a daily basis, there’s actually a scorecard for the company that we look at every day, and it’s got sales metrics, it’s got operations metrics,” Baehner says. “It’s a good general look for how the business is performing on a day to day basis and not just day to day. We can look at today, we look at month to date. We can see year to date with all the various sales metrics, we can look at gross margin, we can look straight across at the operational metrics as well. We’ve got a quick snapshot of the general health of the business every day readily available to us.”