Ellco Etikett modernizes their daily operations
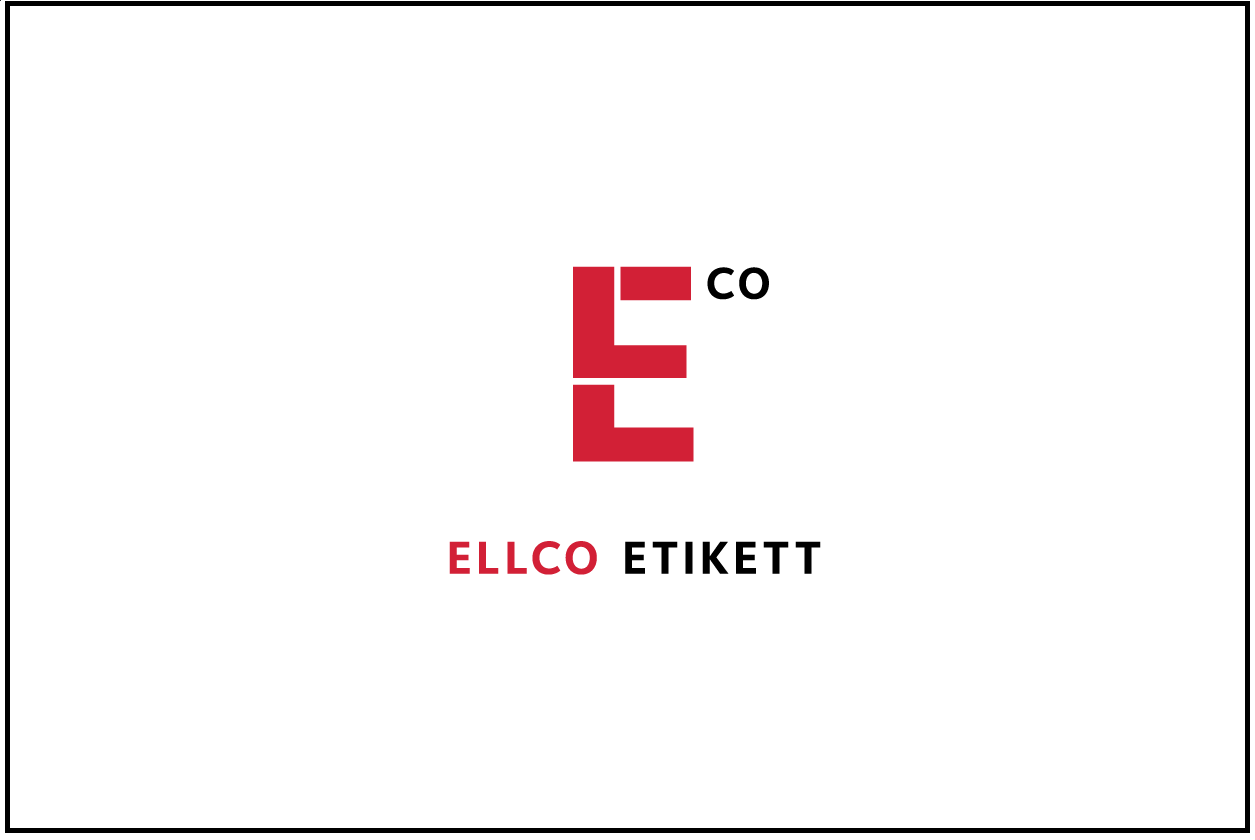
Challenges
- Excessive time with manual operations
- Finding the right ERP for label printers
- Modernizing their daily operations
- Reducing the risk of quality issues.
Results
- Saved time from manual operations
- More transparency with their data and reporting
- Reduction in quality errors
- Better team communication
The Story
Ellco Etikett’s background
Ellco Etikett, founded in Norway in 1985, is an operation of 25 employees. With about a 7 million Euro annual turnover, Ellco has a mix of direct and distributor customers, a diversified market base, and focuses on blank to heavily embellished labels.
Ellco Etikett’s journey to Label Traxx
Ellco Etikett adopted Label Traxx in 2015, after deciding to modernize their operations. Their journey led them to evaluate various systems that were specifically tailored for label printing. Drawing from their experiences with previous systems that fell short of their specialized needs, they conducted a thorough analysis of three or four potential candidates. This process was aimed at finding a system with a proven track record in the label printing industry.
From manual work to reliable systems
One of Ellco’s challenges was evolving from their combination of ERP and manual way of accomplishing daily tasks.
“What I saw as soon as I got into order entry, customer relations, we had a very strange mix of doing things manually and using our previous ERP system,” says Christian Egedius, CEO of Ellco Etikett. “So what I saw was that we hadn’t been able to finally get rid of the old way of doing things. So the estimators, or the employees who knew how to make an estimate, they were really doing that manually.
Ellco had invested in an ERP, but their operations relied on one that was not created for label printers.
“There was the huge Microsoft platform and then the plugin that were supposed to be working well for label printing, but it really wasn’t,” Egedius says.
Reliable data, better job estimating
Ellco found that having more reliable data, through their adoption of Label Traxx and Batched, caused them to rethink their job estimating process.
“One of the things we saw when we really started collecting the data was that the speed we thought we would get off the press was not the same as reality showed us,” Egedius says. “We had to rethink the way we estimated jobs. The old thinking was: ‘Okay, this press can run that 100 meters per minute. So this job can take more than 60 minutes.’ And then we realized that that the average speed was 40.”
Saving time, greater transparency
Ellco Etikett found that adopting Label Traxx as an MIS/ERP helped them save time in their daily operations.
“I think the easiest [improvement] is you save time,” Egedius says. “You reduce the risk of quality issues.”
They also found that their Label Traxx adoption helped with greater transparency.
“We spoke about transparency, and I think that’s maybe the biggest [soft improvement],” Egedius says. “Especially after we got Batched — everyone has access to the same data. The same reports, the same plans.”